

Maker's mark encourages responsible drinking. Alcohol should be consumed in moderation. By entering this website, you are agreeing to our Terms and Conditions, Privacy Policy and Cookie Policy.
MAKER'S MARK®:
BOURBON MAKING PROCESS
We've been making our whisky one bottle at a time in the same distillery since 1953. A lot has changed around here, except how we make our whisky.
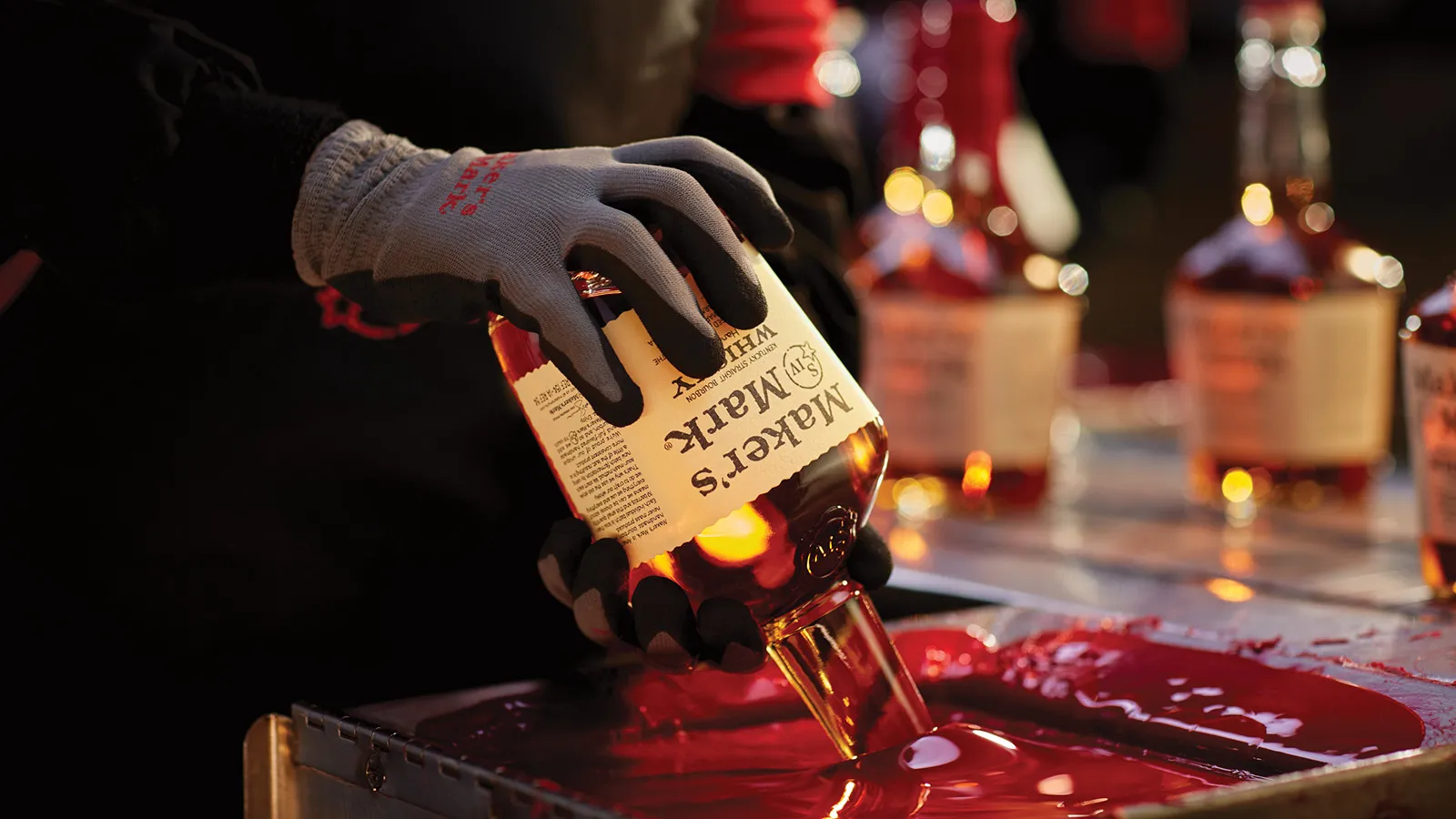
Fermentation
Red Winter
Wheat & Bill's
Mash
In a day when distillery's rye was the go-to grain for whisky makers, Bill Samuels, Sr. found the taste he wanted in soft red winter wheat - making it the star of our mash bill.
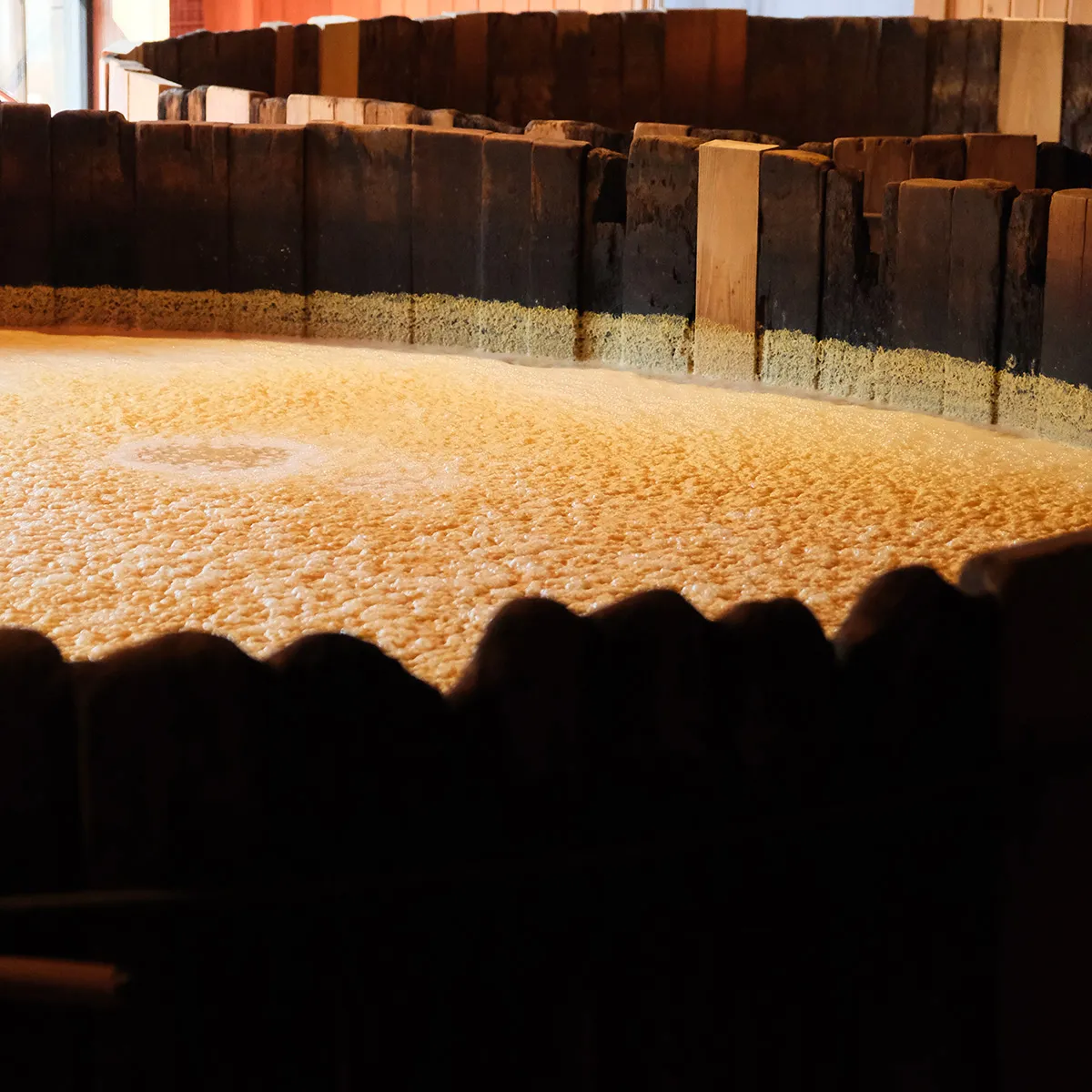
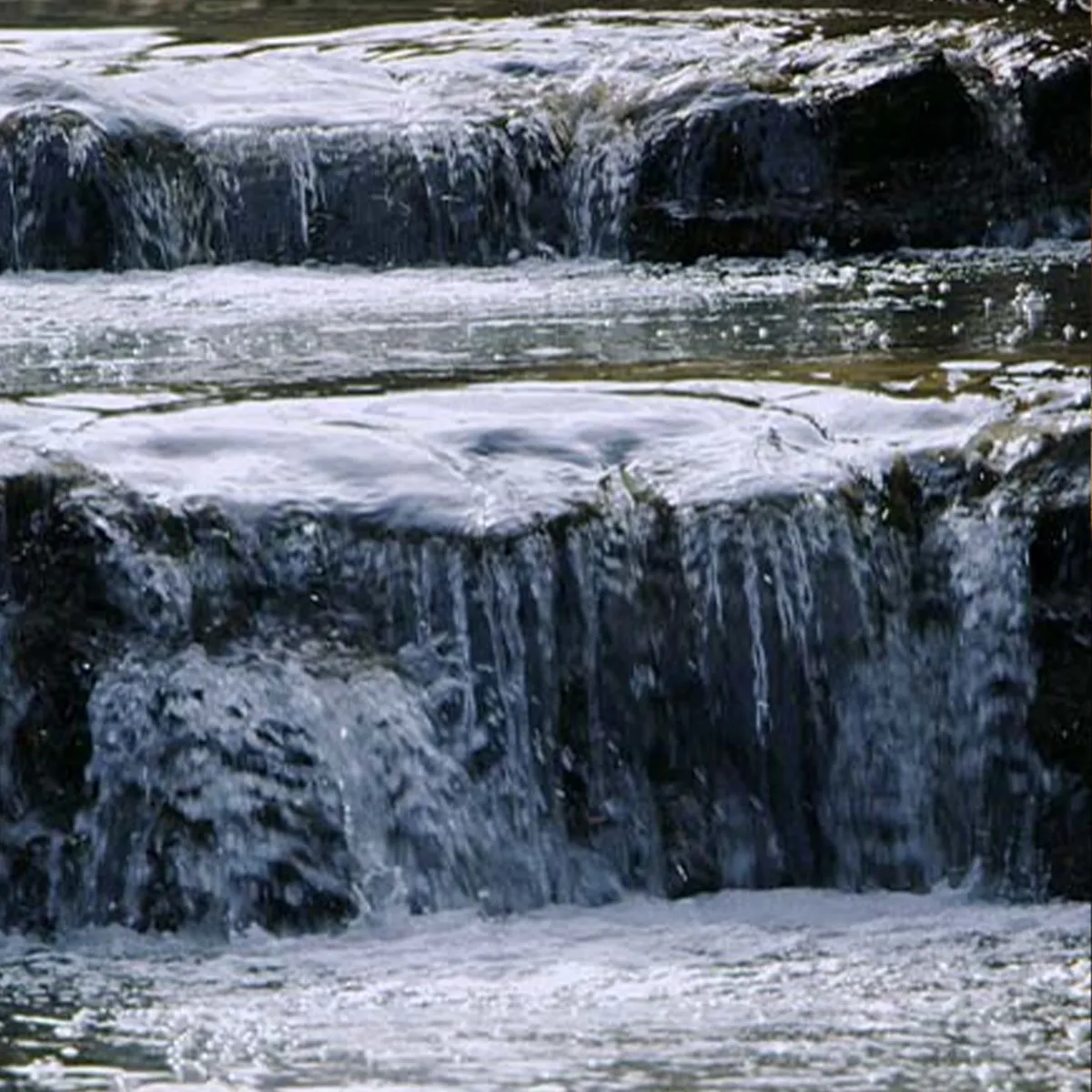
Pure limestone
water
The limestone shelf near the distillery is key to crafting our unique taste. The pure calcium- and magnesium-rich water makes better drinking water and a better sour mash in which yeast can flourish.
A yeast strain as old as Maker's® itself
Sometimes the best, freshest ingredient available is an heirloom yeast strain that's more than 60 years old. This highly guarded microorganism has helped craft every bottle of Maker's Mark ever produced.
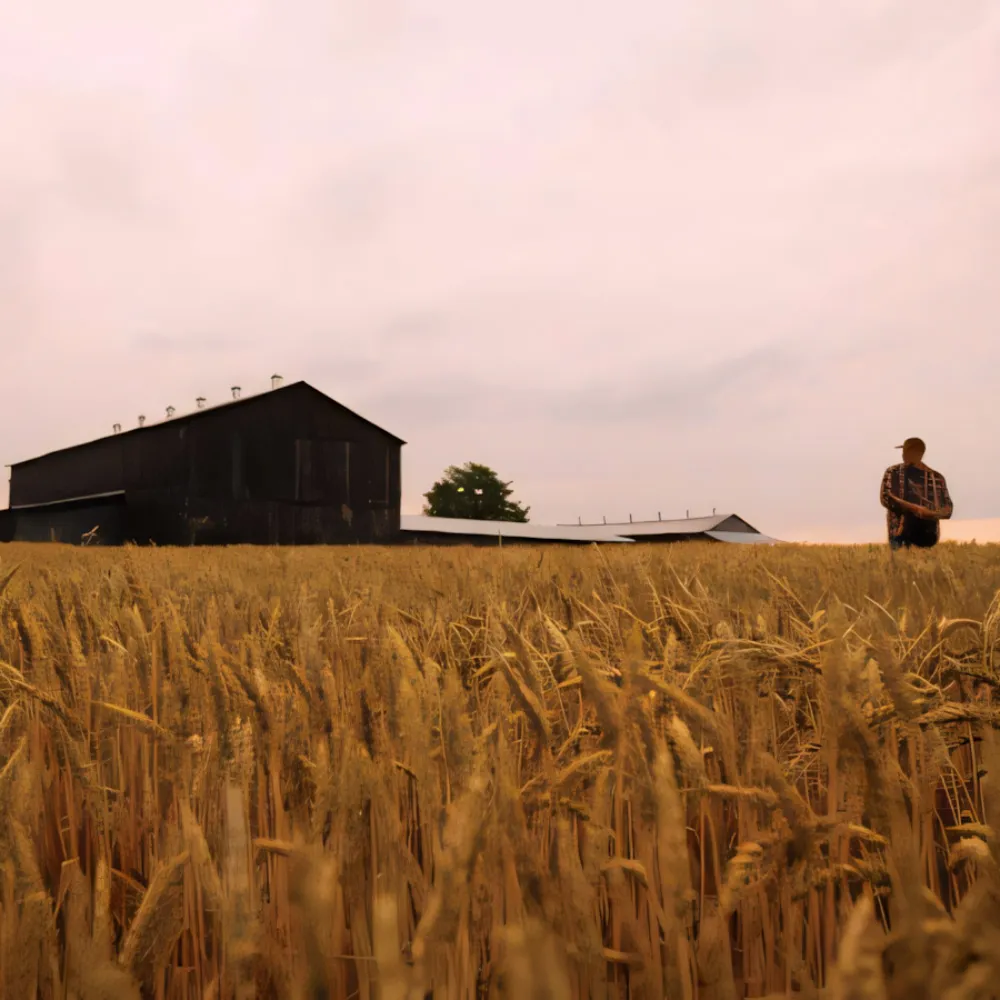
Distillation
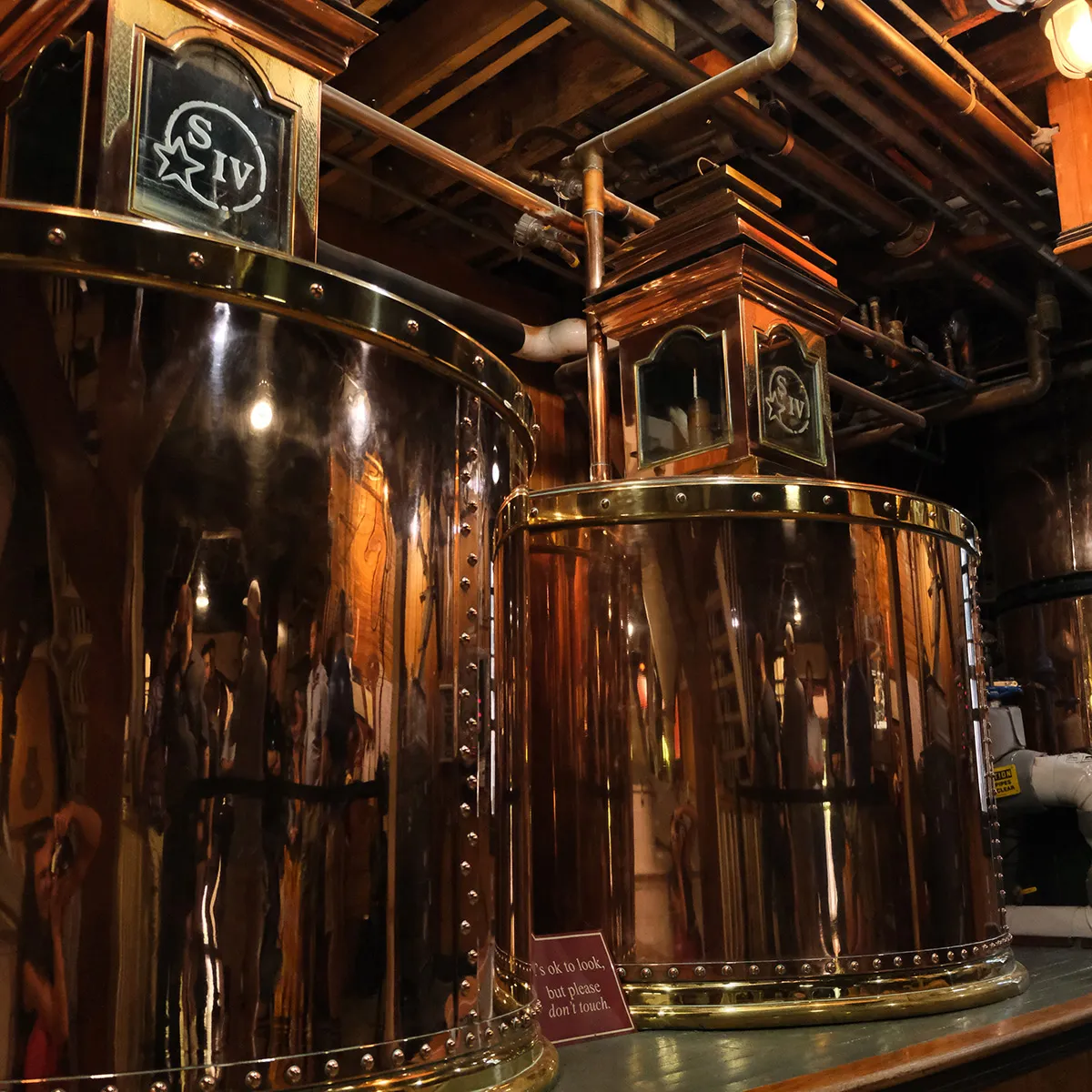
Our column
copper
distillation
stills
These gleaming copper stills are key to our double-distillation process, which removes most impurities for a more refined sipping whisky. Thanks to our friends at Vendome Copper & Brass Works, every drop of Maker's is still made the same way as Bill intended.
Aging
We age to taste not time.
The perfect
degree of char
The process of firing barrels opens pores in the staves and caramelizes the natural wood sugars. This helps give Maker's Mark those pleasant vanilla notes. But before the firing can happen, the cooperage (or barrel-building company) must "season" the new American white oak outdoors for nine months, plus one Kentucky summer, to remove the bitter tannins in the wood that would otherwise go into the bourbon.
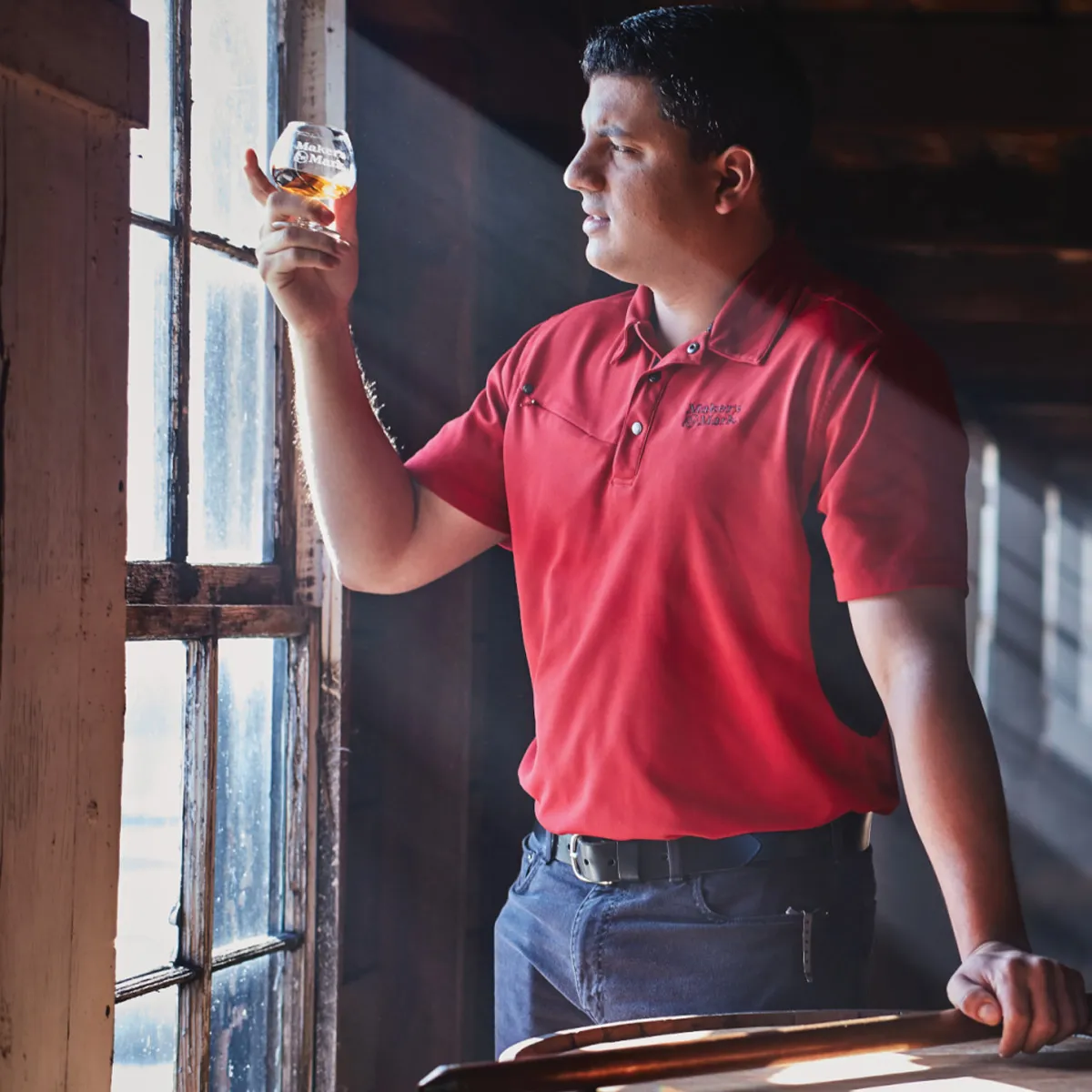
Barrel rotation
by hand
We rotate our 525-pound barrels by hand to ensure proper exposure to the different temperatures around the rackhouse. This adds consistency from barrel to barrel while setting us apart from distillers who abandoned the practice long ago.
Finish
Adding our signature.
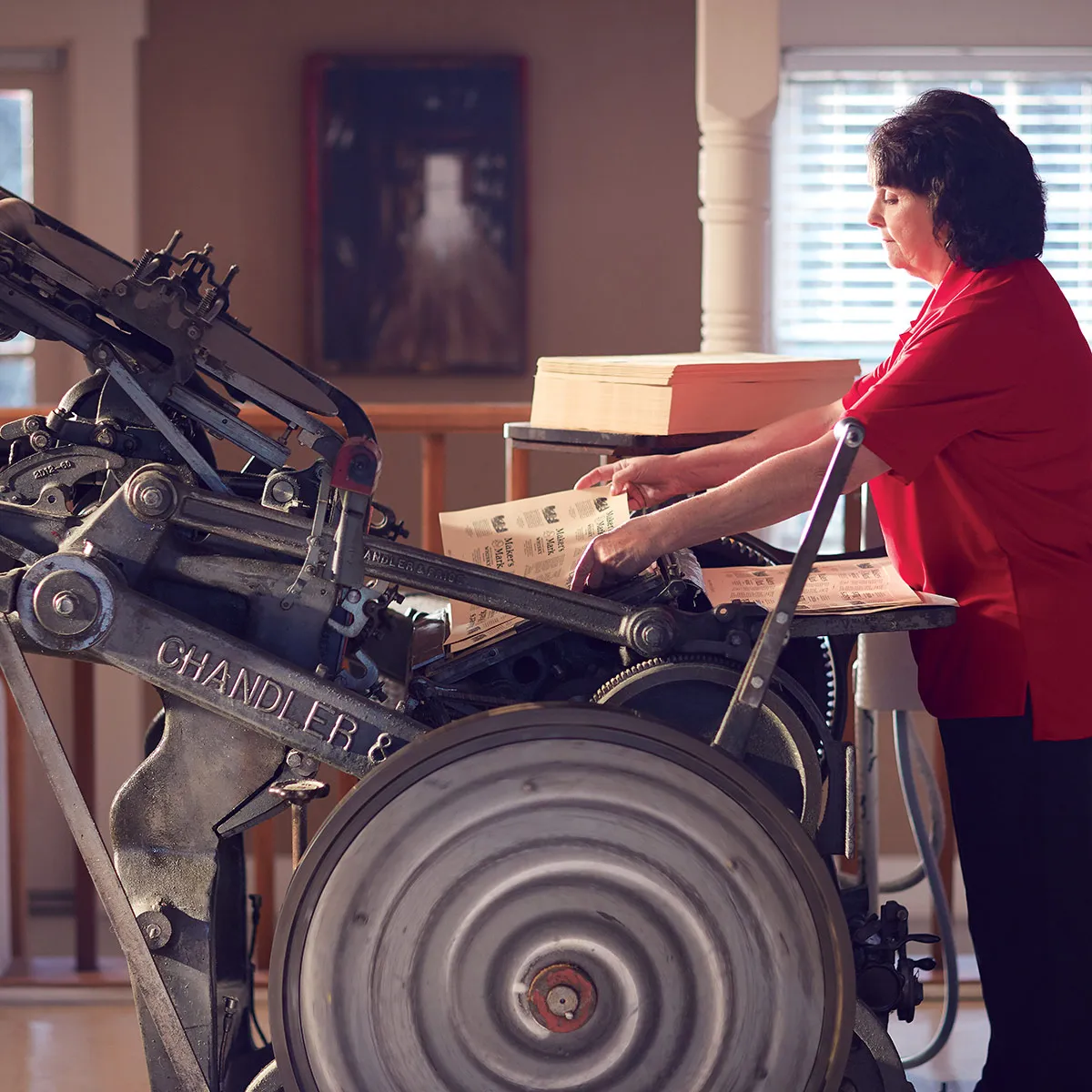
Wax & Label
Cutter
You can still check out the various dipping styles of the folks on our dipping line, from the skinny dipper to the no-nonsense dunker. You can even express your style by dipping your own bottle of Maker's Mark at the distillery. Our distinctive labels – another Margie Samuels original – are still cut on a hand-operated, 1935 Chandler & Price printing press.
Age to Taste
Maker's Mark isn't satisfied simply setting a clock. That's why we age to taste, not time. It usually takes between six to seven years for the whisky to be ready.
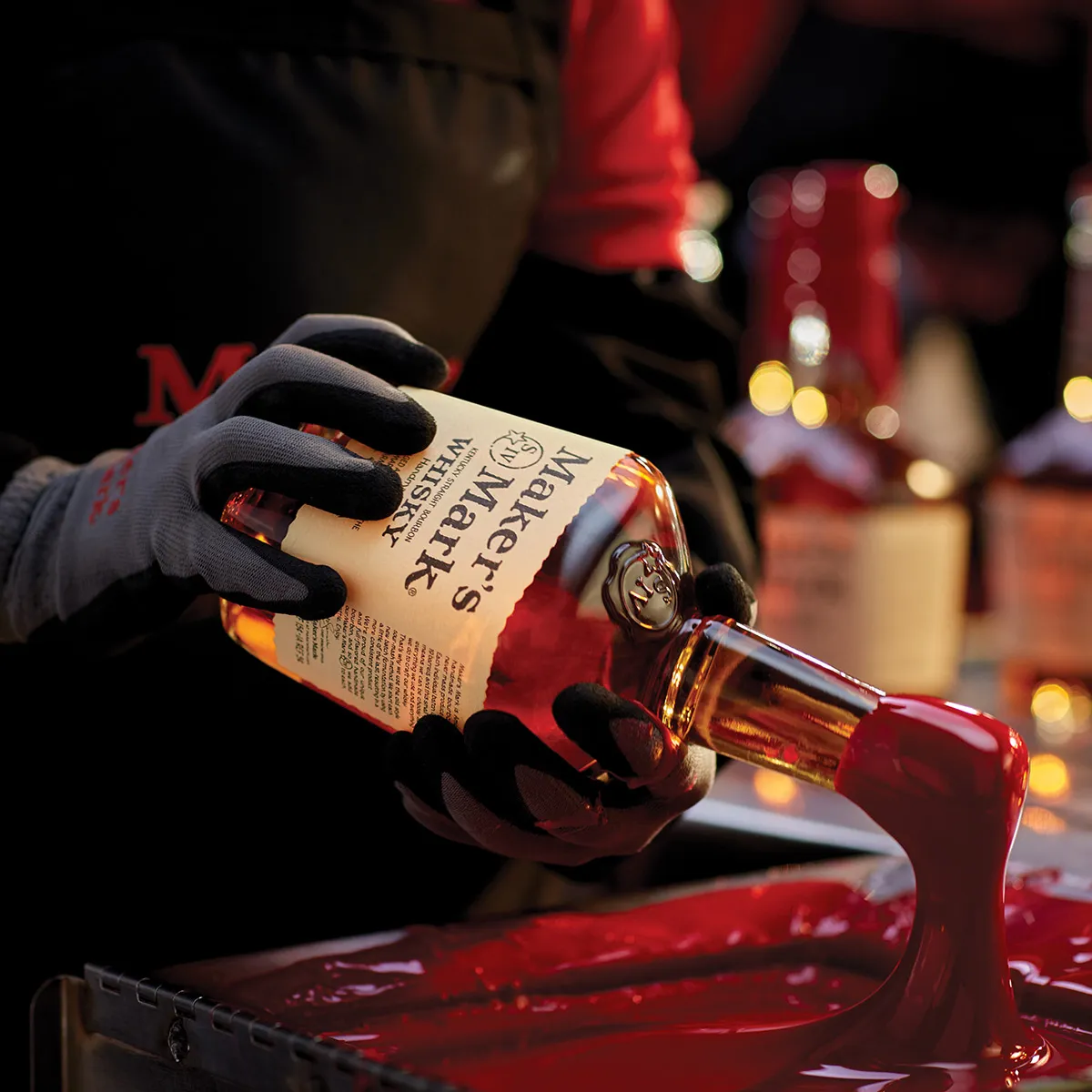
BOLD FLAVOR GENERATIONS IN THE MAKING
Smooth, full-bodied flavor and a distinct hand-dipped red wax seal define our bourbon bottles.
More to Explore